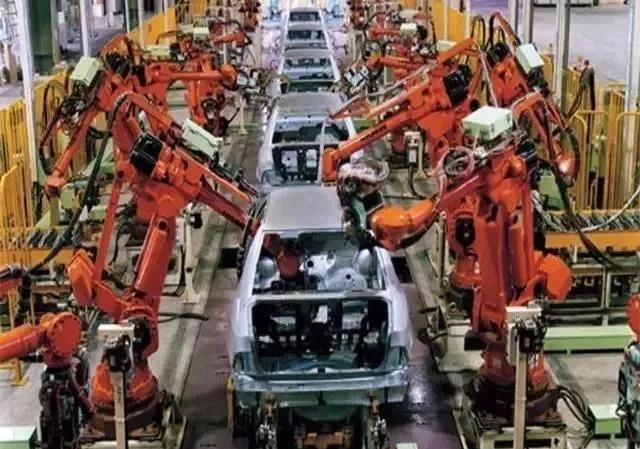
Driven by the “Double Carbon” goals, the new energy vehicle industry has witnessed explosive growth, and market competition has become increasingly fierce. How to improve product performance while reducing production costs has become an urgent problem for new energy vehicle enterprises. As the “mother machine” of industrial manufacturing, machine tools, with their continuously innovated technologies, have opened up new development paths for new energy vehicle enterprises.
With the increasingly prominent demand for lightweighting in new energy vehicles, lightweight and high-strength materials such as aluminum alloys and carbon fiber composites have been widely used. Traditional processing methods are difficult to meet the processing requirements of these new materials, but special processing machine tools excel in this regard. For example, ultrasonic vibration machining machine tools can effectively reduce problems such as delamination and tearing during the cutting of carbon fiber composites, ensuring the processing quality of components. High-speed five-axis machining centers, with their characteristics of high rotational speed and high precision, can quickly complete the milling of complex aluminum alloy components, significantly improving production efficiency. The application of these advanced machine tools not only ensures the machining accuracy of new energy vehicle components but also greatly shortens the production cycle and reduces the time cost of enterprises.
In the wave of intelligent manufacturing, machine tools are deeply integrated with digital and intelligent technologies, bringing a brand-new production mode to new energy vehicle enterprises. The sensors and control systems equipped on intelligent machine tools can real-time monitor parameters such as temperature and vibration during the machining process. Through big data analysis, the machining process can be adjusted in a timely manner to avoid the generation of defective products caused by abnormal parameters. At the same time, based on digital twin technology, enterprises can simulate the machining process of machine tools in a virtual environment, optimize the machining plan in advance, and reduce trial-and-error costs. For example, after a new energy vehicle enterprise introduced an intelligent machine tool production line, the product qualification rate increased by 15%, and the production efficiency increased by nearly 30%.
The continuous innovation of machine tools has also promoted breakthroughs in new energy vehicle manufacturing processes. Additive manufacturing machine tools, namely 3D printers, have broken the limitations of traditional processing and can manufacture components with complex structures and optimized performance, such as integrally cast vehicle chassis, reducing the number of components and assembly processes and improving the overall performance of vehicles. In addition, precision electrical discharge machining (EDM) machine tools play a crucial role in the manufacturing of motor molds for new energy vehicles. By precisely controlling the discharge process, high-precision and high-surface-finish molds can be machined, providing a guarantee for the efficient and stable operation of motors.
In the future, as the new energy vehicle industry moves towards high-end and intelligent development, machine tool technology will continue to iterate and upgrade. The coordinated development of the two will surely inject stronger impetus into the new energy vehicle industry and lead the industry to a new blue ocean of high-quality development.